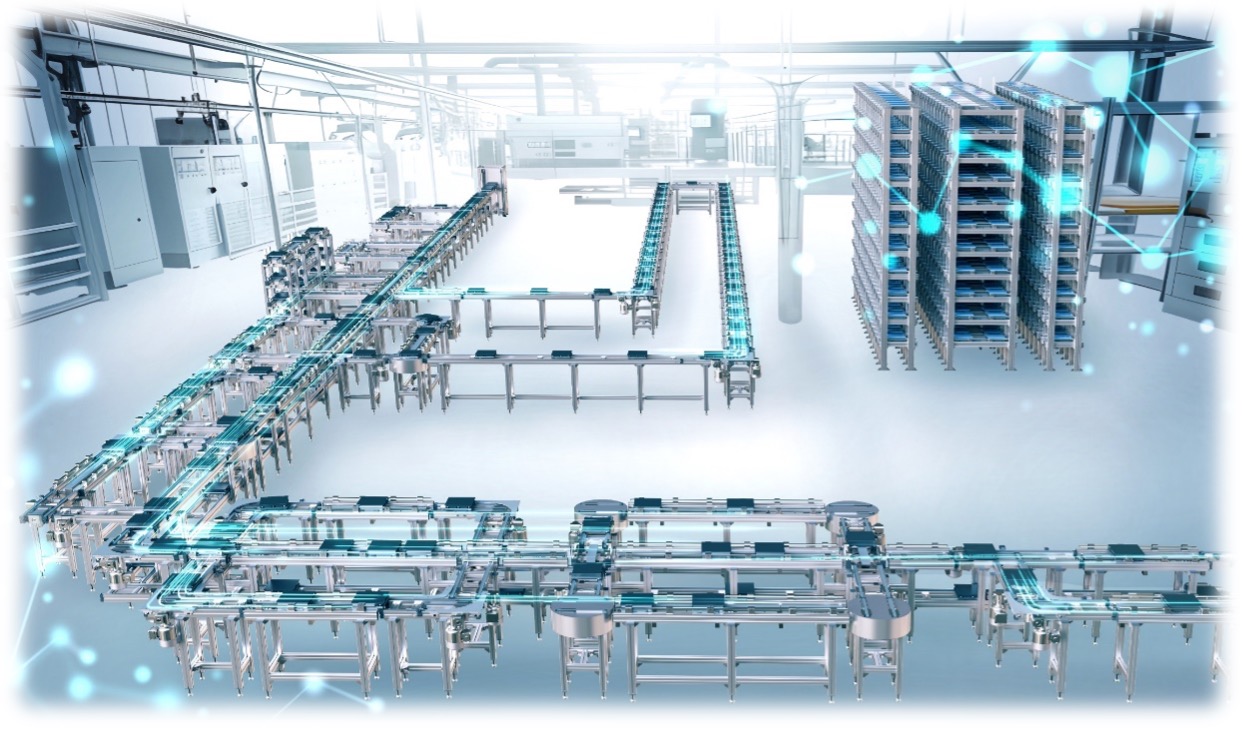
通过智能磁驱输送系统与 AI 深度融合,有望重构工业生产的底层逻辑。
智能磁驱技术为工业 AI 注入新活力
在全球制造业向智能化转型的浪潮中,传统产线面临的效率瓶颈、维护成本高企(非计划停机损失占比超 20%)、柔性响应滞后等痛点日益凸显。如何让生产线真正 「聪明」 起来,实现从设备状态监控到预测性维护(PdM)的跨越?近年来兴起的磁驱输送技术给出了一个基于磁驱高频数据采集的创新答案 —— 通过智能磁驱输送系统与 AI 深度融合,有望重构工业生产的底层逻辑。
智能磁驱输送技术是基于电磁学操控的基本原理,结合智能运动控制算法实现复杂工业场景下的高柔性精密输送的一项全新技术。该技术在很多技术原理角度非常相似磁悬浮列车的基本原理,磁驱输送系统则是将这一技术做小做精用到了工业生产的产线升级上,可以实现高柔性、高速、高精度的运动控制能力,革新全行业工业生产线的使用体验。
2015 年以来,德国倍福、贝加莱、美国罗克韦尔等国际自动化巨头相继推出磁驱输送类产品,并在欧美工业市场上快速扩增使用场景,成为近年来最「网红」的新兴工业零部件。中国智能磁驱输送技术的普及开始于 2020 年前后,目前,智能磁驱输送技术已全面渗透至新能源电池、汽车工业、3C 电子组装,半导体、消费等多个行业,成为近年来增速最快的智能制造零部件单品之一。
智能磁驱输送系统示意图(数据来源:Beckhoff 官网)
根据调研数据,中国智能磁驱输送系统市场在 2023 年、2024 年市场规模分别已达 3 亿及 4 亿元人民币,2025 年有望超过 10 亿元人民币,年化增长率超过 100%。而这一赛道在 2020 年之前,在中国可能还是个鲜有客户采购的新鲜行业。
而随着 AI 技术近年来的快速发展,工业 AI 这一概念也开始出现更多演变和落地的可能性。
磁驱数据采集:打开产线运维的 「上帝视角」
智能磁驱系统的磁驱数据采集功能,本质上是为制造业打造了一套 「数字神经系统」。其运动控制系统能够高频捕获磁驱系统中动子的位置(精度 ±0.01mm)、速度(采样率千次 / 秒)、电流波形等核心参数,同时同步采集工位节拍、产品工艺参数、产线运行状态等多维工业数据。这些数据通过边缘计算节点与云端平台的协同,构建起覆盖生产全流程的实时数据中台。
以新能源电池生产为例,传统产线依赖人工巡检(间隔≥2 小时)和间歇性抽检(抽样率<5%),难以捕捉设备运行中的毫秒级异常。而磁驱系统通过每秒数千次高频采样,能够精准识别动子运动轨迹的亚毫秒级偏差,甚至基于时序预测算法提前预判定子轨道模组的温度异常趋势。这种 「显微镜式」 的监控能力,使得设备综合效率(OEE)分析不再依赖经验估算,而是基于亿万级数据点的动态建模。
AI 驱动的智能决策:从数据金矿到生产力跃升
数据采集只是起点,如何让数据 「说话」 才是关键。通过对历史数据的学习,AI 模型能够精准预测设备故障概率,例如当动子电流波动超过阈值且伴随异常振动信号时,维护模型会分层识别故障源(机械系统 / 伺服系统/ 传感器),进而自动触发预警并生成包含维修策略的工单,将传统的 「事后维修」 转变为 「预防性维护」。
行业变革与未来图景:从柔性生产到产业升级
磁驱输送系统的价值远不止于单条产线的优化。其模块化设计和灵活扩展能力,正在重塑制造业的生产范式。例如,在医疗设备制造中,磁驱系统支持无菌环境下的高精度输送,而在 3C 电子领域,其快速换型能力可满足多品种小批量的生产需求。这种柔性化生产模式,使企业能够快速响应市场变化,降低库存成本,同时提升产品定制化水平。
智能磁驱系统作为一个智能制造领域的新兴「网红」产品,有可能会为业内提倡已久的「工业 AI」概念注入新的可能性。目前全球有多家头部工业公司在该领域销量攀升较快,包括德国倍福、德国贝加莱、美国罗克韦尔等,中国国产厂商包括位于苏州的纵苇科技等。在这一次的产品迭代浪潮中,中国厂商凭借更强的成本优势和更丰富的客户生态,有望再次打造出全球领先的标杆性产品力和工业范本。